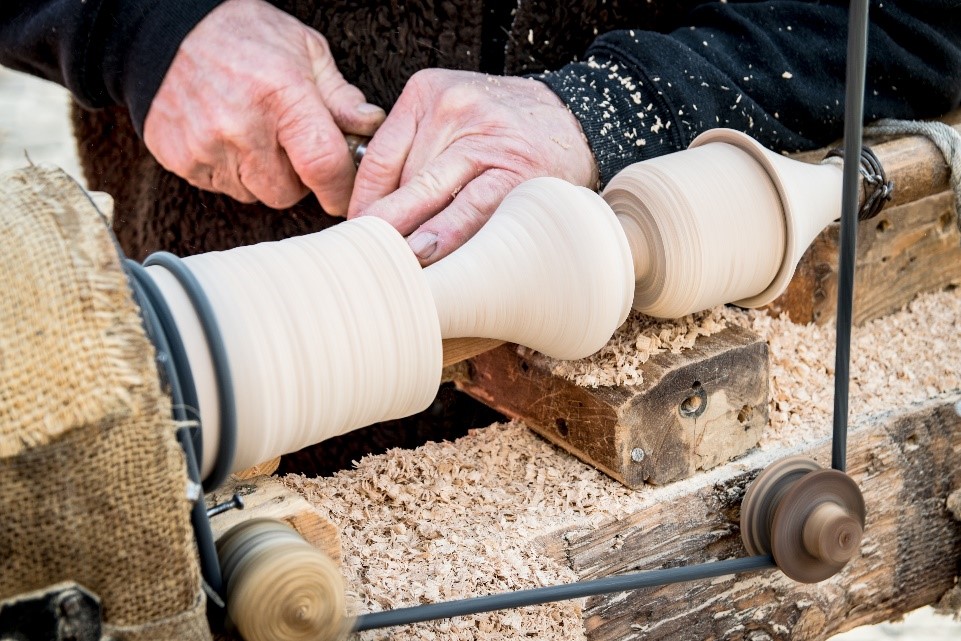
Woodturning is a new art form and you will need the right tools to make it look professional. You can achieve the desired effect with hollowing tools, but it is important to choose carefully. These articles will teach you the basics of Osprey's Hunter, Swan neck, and Hercules. Then, you can move onto the more advanced hollowing instruments. This is a brief history on hollowing tools for those who are curious.
Hunter
Hunter is the name to trust if you're looking for high-quality hollowing tools. These carbide-tools were specifically designed for hollowing and endgrain work. Hunter's unique tool system is centered around a circular structured carbide cutter that lasts 100 times longer than comparable HSS cutters. This tool doesn’t need sharpening and can also be rotated to create new cutting edges when necessary.
Hercules
The Hercules Hollowing Tool has many uses. It can be used for making interrupted cuts, or roughing out bowls. Square bodies are designed to spread shock impacts across the rest of the lathe and the ways it works. The 45-degree flat of the shank ensures a stable cut, even when interrupted. This tool comes in two sizes: 5/8" or 3/8".
Osprey
Osprey hollowing tool are great for smoothing out your bowls. They are available in two different sizes and come with a T-9 flag style Torx wrench for rotating the cutter. They can be used like any other tool and are very popular with pen turners. An Osprey can be a wonderful tool to help you get started in woodturning.
Hercules Swan neck
A Hercules Swanneck hollowing tool allows you to do a variety different cutting applications. The tool is available in three lengths, including the 14" (851H), which is for use with end grain in projects that don't require deep cuts. The 20'' (855H), on the other hand, allows for more reach and the 24", (859H), is made from a substantial section of steel. To use the tool, place the round shank on top of the rest.
Osprey neck of the Swan
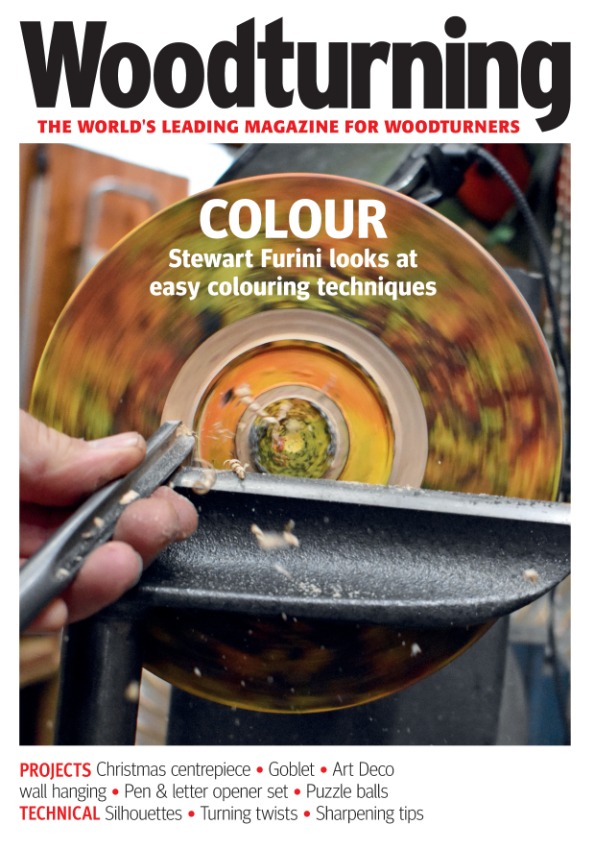
Osprey makes two sets for swan-neck tool hollowing. The swan-neck tools have a unique shape, making them useful for blind turning, undercutting, and side-grain work. The 14 inch (851H version) is best suited to end-grain projects. While the larger (20"'' and 24-inch (8599) tools can be used side-grain and ends-grain respectively, the larger (20"'' and 24-inch (8599) versions are equally suitable. Both tools feature a sturdy steel neck, a long blade and sharpened carbide cutting edges.
Carbide cutters
A carbide tipped carving tool can be a valuable addition to your toolkit. These tools can provide a cutting experience like no other. These tools can reduce strain and improve productivity. Carbide-tipped tools for carving are sharp and last for years. They can be used for all woodturning projects from wood sculpture to hollowing forms.
Simple hollowing system
The Simple Hollowing System for Woodturning takes the tools from the hands of the turning machine and allows the user to direct the cutting process with precision. The system consists of a solid mounting plate, an articulating arm and a laser assembly. This system is compatible with any tool with a 1/2" round handle tang. The cost of the system is $425 and includes shipping. You can also buy optional accessories to complete this system.
FAQ
Can you teach yourself woodworking?
It is best to do it yourself. Woodworking is an art form that requires patience, practice, skill, and experience. Any craft requires patience to master.
To actually learn something is the best way. Start small, and work your way up from there.
Where can I get free woodworking plans?
For free woodworking blueprints, you don’t need to read any magazines or buy any books. All you need to do is search Google. Search Google for "free woodworking" to see hundreds of sites that provide free plans.
How do I identify the type of wood that I am dealing with?
When purchasing wood, always check the label. The label should include information about the wood species and its moisture content as well as whether or not it has been treated using preservatives.
How long does it usually take to complete a piece furniture?
It depends on the wood type you choose, the complexity and the amount you apply to the finished product. Hardwoods require more care than softwoods. Hardwoods also tend to be more expensive than softwoods. But they last longer and resist moisture better. Finishing furniture can take anywhere from one week up to three months.
How often should I get new supplies?
Over time, you may need to replace your tools. Hand tools will need to be sharpened regularly. If you are using power tools, you will need to purchase replacement parts regularly. Avoid buying too many products at once. Spread your purchases out over several months.
Do you have any other information I should know about woodworking and/or the process of making it?
Furniture making is a laborious task. It's easy not to appreciate how hard it is. Finding the right type of wood is the most difficult aspect of this process. It is difficult to choose between the various types of wood.
Another issue is that wood does not have the same properties. Some woods will warp and others will split or crack. You must take these things into consideration before purchasing wood.
Statistics
- The best-paid 10 percent make $76,000, while the lowest-paid 10 percent make $34,000. (zippia.com)
- The U.S. Bureau of Labor Statistics (BLS) estimates that the number of jobs for woodworkers will decline by 4% between 2019 and 2029. (indeed.com)
- If your lumber isn't as dry as you would like when you purchase it (over 22% in Glen Huey's opinion…probably over 10-15% in my opinion), then it's a good idea to let it acclimate to your workshop for a couple of weeks. (woodandshop.com)
- In 2014, there were just over 237,000 jobs for all woodworkers, with other wood product manufacturing employing 23 percent; wood kitchen cabinets and countertop manufacturing employing 21 percent. (theartcareerproject.com)
External Links
How To
How to join wooden boards without using nails
Woodworking is a hobby that many people enjoy doing. You can make useful items from wood with your hands, which is both relaxing and fun. You may need to join two pieces without the use of nails. This article will explain how to do this so that your woodwork projects stay beautiful.
First, remove any sharp edges from the wood pieces before you join them. Sharp corners can cause problems down the line. After you have completed this step, you are ready to glue your boards together.
If you're working with hardwood, you should only apply glue to one side. If you are using softwoods such pine or cedar, glue should only be applied to one side. Press the boards down until the glue is fully incorporated. Make sure you let the glue dry before moving on to the next step.
After you have glued the boards together, drill holes in the joints where you intend to place screws. Depending on what type screw you choose, the size of these holes will depend on how big they are. For example, if you intend to use 1/2-inch wood screws, you need to drill a hole that is at most 3/4 inches deep.
After drilling your holes, drive the screws into the board's backside. Don't hit the board's surface. You could damage the finish. Avoid hitting the screws' ends too often when driving screws. This will prevent splitting in the end grain of the wood.
Now that your project is finished, you'll want to protect it from the elements. You have two options: seal the whole furniture piece or just the top. You'll want a product that lasts for many years. Examples include oil-based varnishes and polyurethanes, shellac, lacquer and others.
These products can be found in most home improvement shops. Be sure to choose the right one for your project. Keep in mind that certain finishes can be toxic and should not be used indoors. Protective gear should always be worn when handling these finishes.