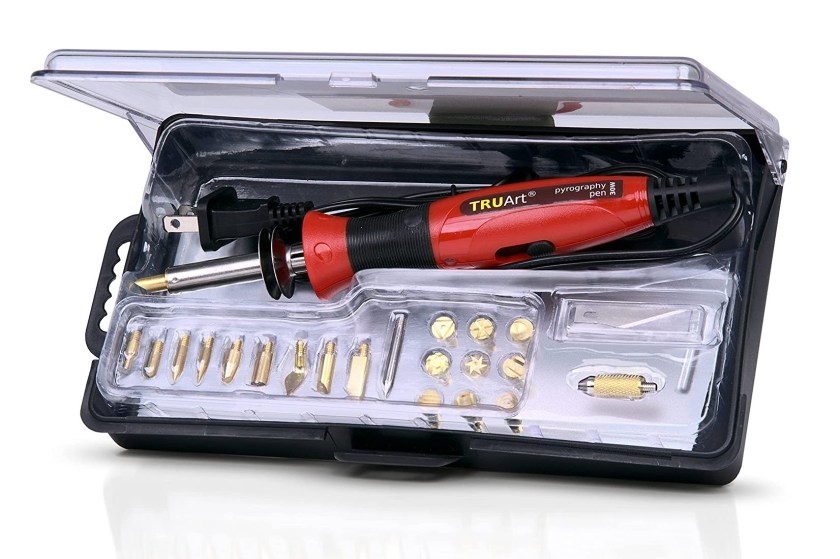
If you are looking to create beautiful and custom pieces for home, you might be interested learning more about pyrography. This ancient art dates back to the 17th century, and is the process of burning intricate designs and decorations into wood. The resultant burn marks create beautiful dark designs. You can also include landscapes and portraits. This method is popular for home decor and has been used for centuries.
Yoko sugi ban
The technique of shou sugiban, which is charring wood's surface, was developed in Japan in the 18th century. This creates a rich charcoal-black color on the wood's exterior, which can also give it an Alligator skin or cracked appearance. For a traditional, rustic look, the Japanese cedar is typically used, but other wood species may be used with varying degrees of success. The wood is protected against future damage by controlled charring, making it an excellent preservation technique.
Shau sugi ban
The method used to remove the char is what makes shou sugiban and traditional Sanding so distinct. Some woodworkers using shou-sugi ban use wire brushes to remove the charred top layer, while others use coarser sandpaper. Either way, you need to scrape enough char away to reveal the brownish-black color underneath. The resulting effect will be an alligator-skin-like pattern, and the sanding process is necessary to remove the excess char.
Shau sugi ban on cedar
While shou sugi ban on pyrography creates an appealing wood finish, it has practical implications. It is possible to track bits of charred lumber throughout a building. They can also be inhaled and inhaled from people who are inside the treated area. To combat this problem, pyrographers are beginning to use propane torch in addition to the traditional wood-burning method. Here are some differences between them.
Yaki sugi ban for basswood
Yokisugi ban on cedar, a centuries-old Japanese method, can increase wood's beauty as well as its durability. Though sometimes referred to as Shou sugi ban, this process involves charring the surface of wood to create a beautiful pattern. The process is so popular in Japan that cedar is used in many shou sugi ban projects. Satoshi Kmura, operations director at a Japanese timber company, describes why shou shugi ban is so common and what it means to woodworkers.
Yaki sugi ban on blue stained pine
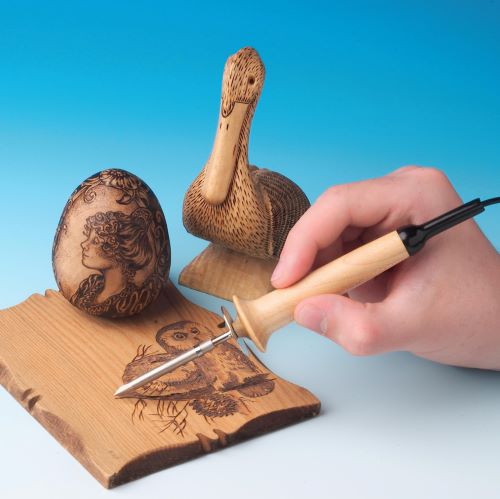
This is commonly known as shou-sugi ban. It preserves wood using fire. Traditionally, cedar is used for shou sugi ban, but other types of wood are also suitable. While cedar is the traditional wood used for this process, yakisugi may be applied to any type of wood. This technique is popular among traditional Japanese craftspeople.
Shau sugi ban on basswood
Charring cedar wood gives it a rich, dark black color with distinctive crackled edges. Cedar is naturally resistant and repels bugs. However, the surface that has been charred can be used to shape wood. There are two options for charred wood: untreated or reclaimed. A cedar panel can also be treated to achieve a subtler burnt wood finish.
Shau sugi ban on jelutong
There are several benefits to shou sugi ban on pyrography on wood. First, it enhances the wood's natural patterns. The thicker carbon layer makes charred wood more durable. This will depend on the type of timber and the environment where it is used. Shou sugi ban can be an eco-friendly option to treatment wood.
FAQ
How do I organize my shop?
First, make sure you have a designated space for tools storage. Make sure your tools are clean and free of debris and dust so they can be used properly. Pegboard hooks can be used to hang tools and accessories.
How do I choose the right tools for me?
It's important to consider your preferences and needs when buying tools. What do you prefer: metal or plastic handles? What size screws and nails do you use most often? Are you more comfortable using power tools than hand tools?
This is a job that I can make a living from.
Yes! Many woodworkers have this ability. According to U.S. Bureau of Labor Statistics (BLS), woodworkers earned a median annual salary of $34,000 in May 2012. This is significantly higher than the national average, which is $31,000 per year.
Can you teach yourself woodworking?
The best way to learn anything is by doing. Woodworking is an art form that requires patience, practice, skill, and experience. It takes time to master any craft.
You can learn the most effective way to master a skill is by actually doing it. Start small, and work your way up from there.
Are there any tips for starting a woodworking enterprise?
It's not easy to start your own woodworking business. You won't mind working hard if your hobby is something you love. Plus, you'll probably enjoy the challenge of running your own business.
You should remember that unexpected issues may occur when you launch a new venture. Unexpectedly, money might run out. Or you might find that your customers aren’t willing or able to pay as much you had hoped. Preparedness is key to survival in such situations.
One tip is to have a separate banking account for your company. You'll be able to track how much money comes in and out.
Statistics
- Most woodworkers agree that lumber moisture needs to be under 10% for building furniture. (woodandshop.com)
- Overall employment of woodworkers is projected to grow 8 percent from 2020 to 2030, about as fast as the average for all occupations. (bls.gov)
- Average lumber prices rose about 600 percent between April 2020 and May 2021. (familyhandyman.com)
- If your lumber isn't as dry as you would like when you purchase it (over 22% in Glen Huey's opinion…probably over 10-15% in my opinion), then it's a good idea to let it acclimate to your workshop for a couple of weeks. (woodandshop.com)
External Links
How To
Tips for driving a nail in wood
It is essential to pick the right size and style of hammer before you can drive a nail in wood. Claw hammers include mallets, claw hammers (sledgehammers), mallets, ball-peen hammers, hatchets, and mallets. Each type of hammer comes with its advantages and disadvantages. A claw hammer, for example, is the best choice if you need to hit nails hard. However, it's not easy to know exactly where the impact will land. A sledgehammer is great for hitting large areas at once, but it's too heavy to use effectively for smaller tasks.
Place your hand flat on the side of your chosen hammer so that the handle rests in your palm. Grip the handle firmly, but don't squeeze it so tightly that you hurt yourself. Your wrist should be relaxed while you hold the hammer straight upwards. Swing the hammer back towards the ground, with your aim at the middle of the nail. You should feel the impact on the nail from the hammer. If you're having trouble getting the hang of swinging a hammer, practice with a block of wood until you get the rhythm down.
Once you are ready to drive the nail, place the hammer close to your body. Place the nail so that it is perpendicular with the wood's surface. Keep your focus on the tip of each nail. Swing your hammer forward. Then follow through with the motions of the hammerhead. Repeat this action several times, gradually increasing the speed of the swing. When you are confident with the technique, add power to your swings. Then, raise the hammer from your shoulder to bring it down. This way, you'll be able to put more energy behind your blows.
Once you've nailed the first hole, remove the hammer from the nail. You can then remove the rest of the nails using a prybar or a screwdriver. Keep the nail heads parallel to the board's surfaces in order to avoid splitting wood.