
If you've ever wanted to try chip carving, then you've probably noticed that it can be a challenging task. There are many techniques and styles that you could try. But which one should you choose? What tools do you need? In this article, I'll share my tips and tricks for carving chips, and help you decide which one is right for you. You can carve potato chips in a traditional or more modern way, but there are some essentials that will help you succeed.
Traditional
Chip carving is one of the oldest forms of decorative woodcarving. You will need a straight-edged blade knife, but you can also use a skew-ground and offset knife. Chip carving involves making small triangular cuts in wood to create patterns. This art form began over 1,000 years ago and evolved simultaneously in many different lands. The designs are often so similar that it was difficult to distinguish between them because of their popularity.
As woodcarving became more widespread, the skills necessary to do the job were handed down from one generation to the next. In Sweden, chip carving was a common way to decorate furniture and eventually schools were established to teach the art. Modern chip carvers are able to benefit from the centuries-old skills and knowledge of carvers. Through the generations, knowledge and experience was passed down from carver to apprentice and student. It's a lifelong process that continues today.
Formulary free
This DVD will teach you how to chip carve. Murray Taylor's DVD shows you how to make freeform and geometric carvings. It is a wonderful introductory project, with lots of information. Both NTSC and English versions are available. The DVD can be purchased in stereo or widescreen. Artisan Media Ltd. is the owner of DVD. It is also available in MP4 format for Windows or Mac computers.
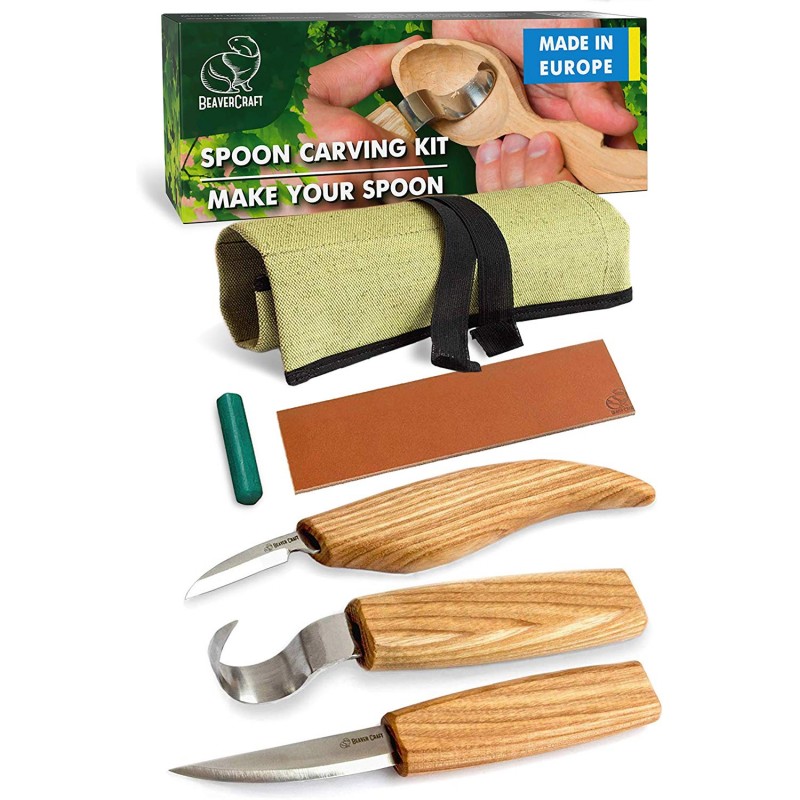
Geometric chip carving is based on lines, circles, triangles and circles. This technique is flexible and can be used in a variety of styles. This style of chip carving is also referred to as free form chip carving. You can make your chips look beautiful in any room, no matter whether they are a flower, a dragon or a tree. A free-form method of chip carving is a great way to incorporate several different techniques into one piece.
Techniques
Chip carving has been around for centuries. You can find examples in many countries around the globe. Chip carvings have been discovered on paddles and handles for ceremonial tools in the South Pacific Islands. The carvings were likely made using pieces of bone and seashells, although some people also used shark teeth. This book will show you how to create amazing designs by using different chip carving techniques.
It is simple to carve chips if you follow a few basic techniques. The first is to understand how to carve the fine Triangle. This pattern is easy to understand and easy to execute. To carve this pattern, you simply need to carve various triangles and repeat this process over again. However, chip carving doesn't have be boring. Variation of the triangles can give you a wide variety of patterns.
Tools
Lora S. Irish will provide a free online seminar on chip carving. She will show you how to use various carving tools, including a stab knife, chip knife, and detail bench knife. Irish will also be demonstrating the different types and uses of wood carving tools. You can choose from the list below to purchase the right tool for your carving needs. These tools can be used for creating simple shapes and designs or to make intricate designs.
Chip carving knives require special geometry. It measures approximately one-half inches in length and has a narrow, curved edge at the back. This allows you to make precise incisions. You should also choose a point that is sharp and needle-sharp so that the edges meet perfectly. You can also get chip carving knives made out of stainless steel. They have a sharp tip. A chip carving knife should be sharp enough to cut a sliver of wood.
Getting started
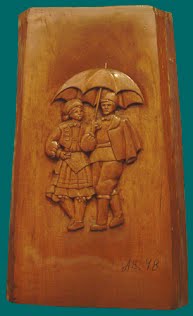
First, learn about chip carving. This will vary depending on the type or carving you do. Nevertheless, you should be aware of some basic principles to ensure that your work is as accurate as possible. Chip carving is a technique that involves creating a fine pattern in wood. To create your first chip carving, follow these steps:
When using a chip carving knife, it is essential to sharpen it well. A chip carving knife's blade will have bevels at each end. This indicates that it is primary. The sharpening tool is shaped like a small diamond and can produce sharp edges. It should be placed at a 10-degree angle. It will also sharpen your chip carving knife as well as your chip carving tool simultaneously.
FAQ
Can this be a way to make money?
Yes! Many woodworkers are already doing so. According to the U.S. Bureau of Labor Statistics' (BLS), in May 2012 the median annual wage of woodworkers was $34,000 This is higher than the $31,000 annual national average.
Which wooden items are very popular?
These wooden products are the most popular. They were made from sustainably harvested wood.
Most furniture is made from oak, maple, mahogany or walnut.
These woods have beautiful grain patterns and colors. They are also very strong. They will last for many years, if taken care of properly.
Wooden furniture should always be painted first to protect against moisture damage. This includes all surfaces, including drawers, doors, and handles.
A paint that resists water is the best choice to ensure that furniture lasts a long time.
A high-quality oil-based primer should be used, followed by two coats with top coat. Depending on how much wear you expect, you might need to apply more coats of topcoat.
Avoid spray cans or aerosol colors. These products have solvents that evaporate quickly, leaving behind dangerous fumes.
Can I refinish furniture that I make?
Yes! There are many different ways to refinish older furniture without the need for professional help. Here are a few ideas:
To remove stains and scratches, use sandpaper. Finally, use a clean cloth or sponge to clean the surface.
Clear polyurethane varnish should be applied. Allow to dry thoroughly before moving furniture.
Use acrylic paint to paint furniture.
Use stain instead of paint. The furniture will get a rich look with the stain.
Apply shellac wax. Wax will protect the wood and add shine.
Where do you start when it comes to woodworking?
The best way to learn how to build furniture is by building furniture. You'll need tools, and you'll have to make mistakes along the way, but if you keep at it, you'll eventually figure out what you're doing.
Choose a project that interests you. It can be something as simple and small as a box, or large-scale as an entertainment center. After you have decided on a project to work on, contact a local woodworker that specializes in this type of work. Ask your local woodworker to help you determine the right tools for you and where they are located. It's possible to ask your friend if they do this type of work.
How does a beginner woodworker earn money?
Many people are looking to create their own furniture and start an internet business. If you are just starting to build furniture, there are many other ways to make money than selling on Etsy. You could sell at craft fairs or local events. Offering workshops could be another option for those who are interested in learning how to build their furniture. If you have the experience to be a carpenter, builder, or a designer, you may consider offering your services in remodeling homes or creating custom pieces.
Statistics
- In 2014, there were just over 237,000 jobs for all woodworkers, with other wood product manufacturing employing 23 percent; wood kitchen cabinets and countertop manufacturing employing 21 percent. (theartcareerproject.com)
- If your lumber isn't as dry as you would like when you purchase it (over 22% in Glen Huey's opinion…probably over 10-15% in my opinion), then it's a good idea to let it acclimate to your workshop for a couple of weeks. (woodandshop.com)
- The U.S. Bureau of Labor Statistics (BLS) estimates that the number of jobs for woodworkers will decline by 4% between 2019 and 2029. (indeed.com)
- Average lumber prices rose about 600 percent between April 2020 and May 2021. (familyhandyman.com)
External Links
How To
How to make wood joints
This tutorial will teach you how to join two pieces wood together. We will use the pocket hole joint, which is drilling holes in the wood to join them. This works well if the wood is straight and smooth. You might consider dowel joinery if your wood isn’t straight or flat. These are the steps
-
Drill Pocket Hole Joints. You will need to measure and mark the exact location of your pocket hole joint. Then drill 3/4 inch deep holes into the ends of each piece of wood using a jig saw or handheld drilling machine.
-
Sand Smooth. You can sand the edges of the wood to ensure that it doesn't split.
-
Glue together. Apply glue to both the ends of the wood. Let it sit for about 5 minutes before clamping the pieces together.
-
Connect the pieces. Once the glue has dried, clamp the pieces together so they are flush.
-
Trim Joinery. Trim the excess wood around the joint after the glue has dried completely.
To be able to turn the pieces inside-out, leave enough room between them.