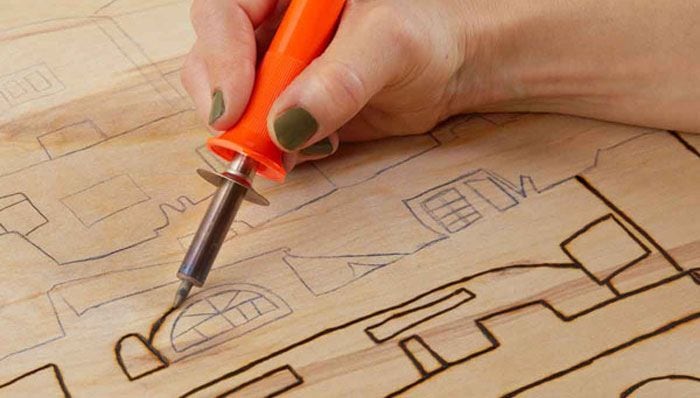
If you're going to create graphite artwork, it is crucial that you choose the right kind of transfer paper. This article will explain the differences between graphite and Saral papers. The article will also cover the benefits of each paper. Graphite paper, especially when it comes to portraits, is a wonderful choice for creating works of art. However, it is important to remember that this type of paper requires special care.
Graphite transfer paper
Graphite-transfer paper is a unique type of paper that features a layer graphite one side. This paper works just like carbon paper and can be used to make copies. If you're not good at drawing, this is a great way to preserve your drawing while speeding up your painting practice. You can also use graphite to make outlines and designs that you can erase later.
Avoid fingerprints on the transfer paper when using graphite pencils. This is perfectly acceptable while working, but not so ideal when storing your work. Your graphite-covered transfer papers should be stored in pairs. Place them in a filing folder. You can place larger sheets face down if they are large. Just be sure to use proper ventilation! This will guarantee you the perfect graphite copy paper every time.
Transfer paper
Arteza sells graphite transfer papers to transfer your artwork onto canvas. They come in convenient sheets of nine-by-13 inches. These papers make it quick and simple to transfer your designs to canvas. The 60 sheets include professional-grade graphite papers. Important to remember that your design should be transferred using consistent pressure. Pressing too hard can cause your artwork to rip through the paper or canvas.
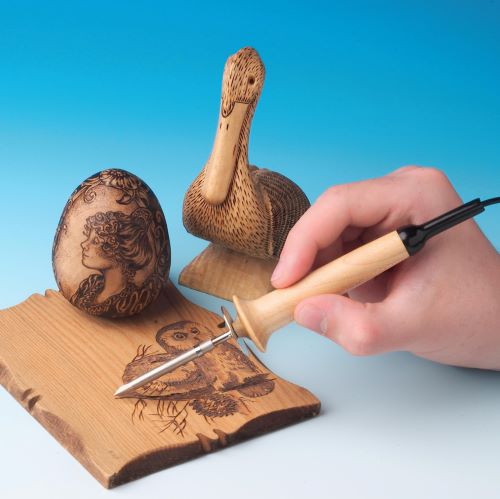
Graphite transfer paper comes in many shapes and sizes. They can be used as-is or you can cut them into grids to cover a whole wall. They are made with enough graphite that it will not smudge or leave a thin trace. When you have finished transferring your drawing, simply use a kneaded eraser to erase any remaining marks. The graphite sheets cost about $25 per ten sheets.
Saral paper
Saral paper is the first commercially-produced transfer paper. Developed by Sara Albertis in the 1950s, Saral paper produces clean, non-glaring marks that can be easily transferred to most surfaces, including fabric and wood. Saral paper comes in convenient rolls or four-sheet sets. They measure twelve inches wide x three feet long. Saral paper, also called tracing papers, is also available. Here's how to use it:
Saral paper's lighter weight makes it ideal for transfer patterns and designs between surfaces. It is especially useful to graphic designers as well as watercolor artists. Graphite is best handled with gentle pressure. If you apply too much pressure, it can damage the paper. Saral's paper transfer comes in a box to protect your artwork. Before applying the transfer paper to your artwork, it is important to carefully read and follow the instructions.
Colored pencil transfer papers
When creating color pencil transfers papers on graphite papier, a soft colored pencil works well. The paper is less scratched and the texture is more soft. To gently remove the remaining grit, you could also use a softener or a kneaded eraser. You can then use a progresso to clean the graphite with a damp cloth. This is how to draw a detailed sketch.
Graphite, though more durable than other options, does leave a darker mark. Graphite papers cannot be used for professional purposes as they require you to use more pressure in order to remove the marks. They are great for classroom demonstrations. Graphite can be reused many times because it doesn't rip easily. And it's very affordable, too!
Graphite transfer sheets
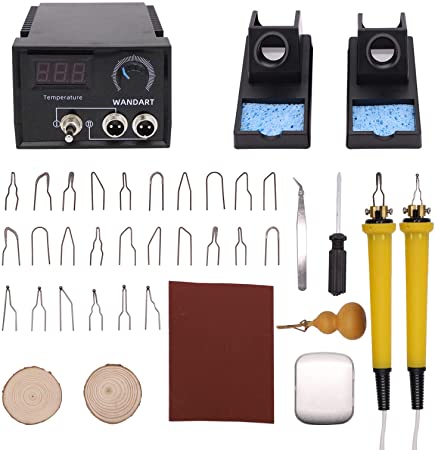
Graphite paper transfer sheets are great for transferring drawings and designs from one surface to another. They are useful for stenciling, tole painting, and many other art and craft applications. They are light and can be used to erase complex tasks. They can also be very expensive if you want to use them on soft surfaces such as paper or fabric. Before you buy them, consider the following factors.
There are different sizes available in graphite transfer sheets. A 20-by-36-inch sheet can be used to trace a large canvas. These sheets can be traced on a large canvas without needing to be taped or glued. They will leave a mark on porous surfaces but are not recommended. They are also more durable than graphite paper and leave crisp and bold lines. These sheets can also be used for demonstrations and classroom activities. Graphite transfer sheets can be used with a variety if materials and come in a variety of colors.
Transfer sheets for colored pencils
There are many advantages to colored pencil transfer sheets. However, there may be some limitations that make them less suitable for professional-quality work. Heavy lead tends to press harder against the paper so you might need to apply more pressure when transferring lines. If you apply too much pressure, the paper could be damaged and white lines might appear. While lighter-colored pencils may be more durable, they can also leave darker lines on your print.
Graphite-like paper is a great alternative for tracing outlines and complex art. These graphite-like papers can be used on many surfaces, including fabric and metal. They are also wax-free. They also work well with many other surfaces, including stained glass, metal and fine art. They are easily stored in small boxes and can be used immediately. A 12-pack of graphite paper sheets from Sally's would be a great place to start if you are a beginner.
FAQ
What's the difference between a hobbyist and a professional woodworker?
Hobbyists enjoy making things out of wood, whereas professionals focus more on the quality of their work. Hobbyists take great pride in their creations, and share them with family and friends. Professionals will spend hours researching designs before they begin working on a project. They'll be meticulous about every aspect of their work, from choosing the best materials to finishing it perfectly.
Where do I start with woodworking?
Learning how to build furniture is the best method. While you will need tools, mistakes are inevitable, but you will learn the ropes if you persevere.
Start by choosing a project you'd like to complete. You can make a simple box or a large entertainment center. After you have decided on a project to work on, contact a local woodworker that specializes in this type of work. Ask him or her for advice on what tools you'll need and where to find them. You might even ask whether there's someone else you can talk to who does this kind of work.
Which wooden items are very popular?
These wooden products are the most popular. They were made from sustainably harvested wood.
Oak, cherry and mahogany are the most sought-after wood types for furniture.
These woods are extremely strong but also have beautiful colors and grain patterns. They will last for many years, if taken care of properly.
To protect wooden furniture from moisture damage, you should paint it first. This applies to all surfaces including drawers, doors, handles, and handles.
Choose a paint with water resistance if you want furniture to last as long possible.
Followed by two coats, you should apply a quality oil-based primer. Depending on how much wear you expect, you might need to apply more coats of topcoat.
Spray cans or aerosol paints should be avoided. These products contain solvents which evaporate quickly and leave behind harmful fumes.
Do I have the potential to make a decent living doing this?
Yes! Many woodworkers have this ability. According to the U.S. Bureau of Labor Statistics (BLS), the median annual wage for woodworkers was $34,000 in May 2012. This is significantly higher than the national average, which is $31,000 per year.
Statistics
- In 2014, there were just over 237,000 jobs for all woodworkers, with other wood product manufacturing employing 23 percent; wood kitchen cabinets and countertop manufacturing employing 21 percent. (theartcareerproject.com)
- The U.S. Bureau of Labor Statistics (BLS) estimates that the number of jobs for woodworkers will decline by 4% between 2019 and 2029. (indeed.com)
- Most woodworkers agree that lumber moisture needs to be under 10% for building furniture. (woodandshop.com)
- Woodworkers on the lower end of that spectrum, the bottom 10% to be exact, make roughly $24,000 a year, while the top 10% makes $108,000. (zippia.com)
External Links
How To
How to join wooden boards without using nails
Woodworking is a popular hobby. Woodworking is a relaxing hobby that allows you to use your hands to create useful things from wood. You may need to join two pieces without the use of nails. This article will teach you how to do this to keep your woodwork projects looking great.
Before joining the pieces of wood together, you will need to first trim any edges. You don't want to leave sharp corners that could cause problems later on down the road. Now you can start gluing the boards together.
If you are working on hardwood, you should only use glue on one side. Use glue on both the sides for softwoods, such as cedar or pine. Once the glue has dried, press the boards together until they are fully adhered. After applying the glue, let dry the boards before proceeding to the next stage.
After you glue your boards together, drill holes at the joints where screws will be inserted. The size of these holes depends on what type of screw you choose to use. For example, if your screw is a 1/2-inch wooden screw, drill a hole that is at minimum 3/4 inches deep.
Once you've drilled your holes, you'll want to drive the screws through the joint and into the backside of the board. Be careful not to hit the front surface of the board, or else you'll ruin the finish. When driving the screws, try to avoid hitting the ends of the screws too much. This will prevent splitting the wood's end grain.
After your project is completed, you will need to protect it from the weather. You can seal the furniture pieces or cover the top. You'll want a product that lasts for many years. You can choose from oil-based varnishes or polyurethane, shellac and lacquer as examples.
These products are available at most home improvement stores. Be sure to choose the right one for your project. Don't forget to keep in mind that some finishes are toxic. So, always wear protective gear when handling them.