
Chip carving begins with imagining where you want the blade to point. Cut the tile starting at the point and working your way to the larger chips. Do not pull out the chips, but instead gently wiggle them. If there are bits still attached to the tile, you can go deeper. Continue this process until you are satisfied with the finished tile. Next, create your own chip carvings by using a pattern.
Free form style carving
You can carve an image using a split blank or a straight-edged gouge for free-form chip carving. Because its fibers have straight edges, the split blank lets you use more power when carving. You can then cut in both directions by cutting flat the top layer of the wood and removing the bottom layer. Make your own designs and experiment with different templates to enhance your carving.
While carving is a time-consuming process, the rewards of mastering the techniques are well worth the effort. The creation of a design can take twice as long as the actual carving. Chip carving involves many cuts and ridges. It is important to ensure that the ridges are sharp at the bottom. The "sharpness of the ridges, regardless of whether you are carving a circle or not, is crucial.
Using angled cuts
When using an angled knife to carve a chip, you will want to think about what the cut will look like. There will be two sides to the chip. The straight side will be the one. The point of the knife will be placed at the intersections of the two straight walls. A third side cut should be made, and it should match the depth of the two side cuts.
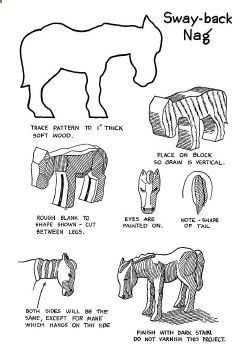
Chip carving works best with lighter wood. This allows for more contrast between the positive spaces and the negative ones. You will see a stronger contrast in shadows if you use lighter wood. Straight chips will highlight the negative space above them, while angled chips will create a subtle shadow that will appeal to the eye. It will appear that the letters have been cut from the wood if your chip is angled.
Using a Flexcut knife
You should invest in a Flexcut knife if you plan to chip carve with a professional-quality blade. These American-made knives have a highly polished edge and come pre-sharpened. However, they should be regularly stropped with Flexcut Gold polishing compound. This knife's ideal bevel angle is 15 degrees. To carve chips, hold it at this angle.
If you're new to chip carving, you might be surprised by the versatility and accuracy of these knives. Every Flexcut knife has a reliable, long-lasting edge. The handles are made of ergonomically-shaped wood. These knives have been designed to give you precise control over every cut while decreasing the chance of chipping. To ensure your carving tools last a long time, Flexcut offers a special coating that prevents chipping by forming a protective film on the blades.
Make a pattern
Start by sketching a design for your chip carving pattern. You can make a pattern that is free-form, or use basic geometric shapes such squares, ovals, or circles. It is vital to maintain straight lines. It might take a few attempts before you get the hang of it. A practice board made from scrap wood can be used to practice the pattern. After you have created a pattern, you are ready to start carving.
If you want to carve a square, you can start by drawing a grid. This pattern will let you play with different designs to create unique pieces. To draw the pattern, you need a pencil and a ruler. Each cell in the grid should be square. Also, the sides should be 3/16" - 1/4". To create triangles, connect one corner of each cell to the opposite to form corners. These can be used to carve three-cornered chips.
Getting started
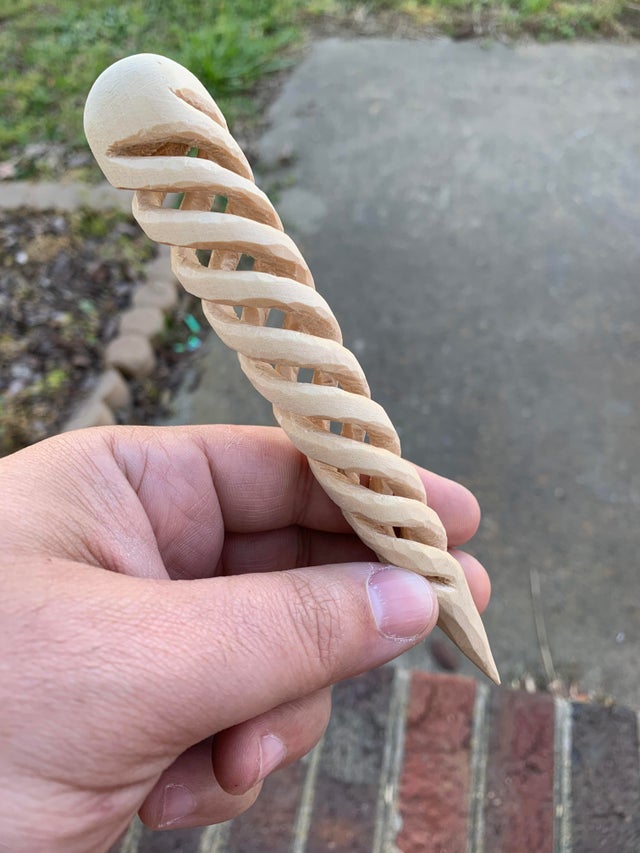
Start chip carving by understanding the basics. The majority of designs are geometric so graphite papers can be used to trace a pattern onto your wood. A ruler can be used to trace along the edge. To erase the lines that you have traced, you can also use an eraser or a hard pencil. After mastering this technique, you will be able to practice it on a larger surface until your grip is good.
Chip carving is very easy to learn and it doesn't cost a lot. Chip carving is very easy to master, compared to other wood carving methods. Chip carving is an easy way for beginners to create beautiful pieces. You can even create personalized pieces for gifts or use in your home. It is a fun hobby that can be passed from generation-to-generation. You can begin by practicing your chip carving techniques on a small piece of wood, such as a wooden spoon.
FAQ
How can I keep my shop organized?
Setting aside an area to store tools is the first step in keeping your workshop organized. Make sure your tools are clean and free of debris and dust so they can be used properly. To hang accessories and tools, use pegboard hooks.
What tools work best for me?
It's important that you consider your needs and preferences while shopping for tools. Do you prefer metal or plastic handles? What size of nails and screws do your hands use most? Are you more comfortable using power tools than hand tools?
How much should a skilled woodworker earn per hour?
Hourly rates for professional woodworkers vary depending on many factors such as skill, experience, availability, geographical location, and other variables.
The hourly average rate for skilled woodworkers runs between $20-$50.
A woodworker with less experience may be able to charge $10 an hour.
How often should I buy new supplies?
Over time, you may need to replace your tools. You'll need to sharpen your hand tools regularly if you use them. For power tools, replacement parts will be required frequently. To avoid buying too much at once, try to spread your purchases out over a few months.
Statistics
- The U.S. Bureau of Labor Statistics (BLS) estimates that the number of jobs for woodworkers will decline by 4% between 2019 and 2029. (indeed.com)
- Woodworkers on the lower end of that spectrum, the bottom 10% to be exact, make roughly $24,000 a year, while the top 10% makes $108,000. (zippia.com)
- If your lumber isn't as dry as you would like when you purchase it (over 22% in Glen Huey's opinion…probably over 10-15% in my opinion), then it's a good idea to let it acclimate to your workshop for a couple of weeks. (woodandshop.com)
- Overall employment of woodworkers is projected to grow 8 percent from 2020 to 2030, about as fast as the average for all occupations. (bls.gov)
External Links
How To
How to join hardwood without using nails
Woodworking is an enjoyable hobby. Woodworking is a relaxing hobby that allows you to use your hands to create useful things from wood. You may need to join two pieces without the use of nails. This article will explain how to do this so that your woodwork projects stay beautiful.
You will first need to trim the edges of your wood pieces before joining them. You don't want to leave sharp corners that could cause problems later on down the road. Now you can start gluing the boards together.
When working with hardwood, glue should be applied only to one side. If you're using softwoods like pine or cedar, you should put glue on both sides. After applying the glue, press the boards firmly until they are completely stuck together. Before moving onto the next step, make sure the glue has dried completely.
After you have glued the boards together, drill holes in the joints where you intend to place screws. These holes will differ depending on the type and size of screw you are using. For example, if you're going to use a 1/2-inch wood screw, then you should drill a hole that is at least 3/4 inches deep.
Once you have drilled your holes you will need to drive the screws through each joint and into the backside. You should be careful not to touch the board's front surface. This could cause damage. Be careful not to drive the screws too hard at the ends. This will help prevent splitting of the end grain.
Protect your finished project now. You have two options: seal the whole furniture piece or just the top. You will want to choose a product that will be durable for many years. Oil-based varnishes are, among others, polyurethanes shellac, laquer, and other oil-based products.
These products can generally be found in any home improvement shop. Make sure you get the right product for your job. Remember that some finishes can be toxic, so you should not use them indoors. When handling certain finishes, wear protective gear.